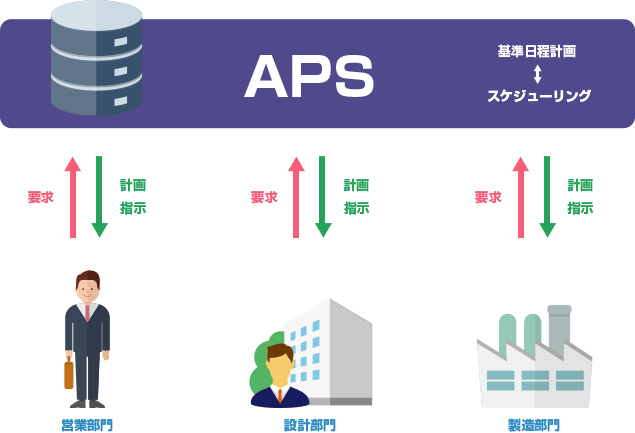
■APSとは
APSは、Advanced Planning and Scheduling の頭文字をとったもので、直訳すると、「先進的な生産計画とスケジューリング」です。
1990年台後半ころ、主にアメリカで使われるようになってきた生産計画とスケジューリングの考え方です。
この時代、MRPを中心にした計画手法に対し、制約の理論(TOC)や数理最適化を応用した方法などが、多数提案されました。これらは総称して、APSと呼ばれるようになりました。
APSは具体的には、
・スケジューリングを先に行う方法
・MRPとスケジューラを連携する方法
・MRPとスケジューラを融合するような方法
・その他独自のアルゴリズム
などがあります。
■APSが生まれた背景
生産計画の方法にはいろいろありますが、システムで行われていた計画方法の主流に、「山積み・山崩し」がありました。これは、MRP(Material Requirement Planning)で資材所要量を計算して、調達計画を定めます。その後、設備やラインへ作業を割り付けるスケジューリングを行います。 この場合、スケジューリングの重点が設備の能力と負荷のバランスだったので、CRP(Capacity Requirement Plannning)とも言われます。
MRPは、固定的なリードタイムを仮定して、設備はラインの能力を無視して、資材の調達計画を計算していました。MRPの計画をそのまま設備やラインの作業割り付けに使うと、ときには能力(Capacity)100%を超えることもあったので、「山積み」と呼ばれました。
それでは困るので、100%を超えた部分を崩しつつ、現場でやり易いように作業を割り振ることを「山崩し」と言いました。
この方式は、「山崩し」する時の余地を残しておくために、「山積み」のリードタイムを長めに設定しておく必要がありました。そのため、仕掛在庫は多くなり、リードタイムは長くなる傾向があります。
アメリカでこの方式を視察したトヨタは、「資源と土地の少ない日本では、同じことはできない」と思いカンバン方式を考え出しました。
大量生産時代から、徐々に短納期化や多品種化が始まると、「山積み山崩し」の弱点が問題になってきます。これに対し、さまざまな対策案が考案されました。
最も古典的な対策案はMRPⅡ(MRP2)です。MRPのリードタイムを短めに設定して、山崩しを試みます。余地が少なくて、うまく崩せなかったら、リードタイムを少しだけ伸ばして再度MRPからやり直し、何度もこれを繰り返すというアイディアです。しかし、計算時間の問題などから、あまり普及はしませんでした。
ゴールドラット博士が提唱した、TOC(Theory Of Constraint)では、ネック工程(制約工程)の作業計画を最初に決めて、前後の作業計画や調達計画は、それに合わせて決めます。シンプルながら、強力な方法で、人気を博しました。考え方を物語仕立てで解説した「ザ・ゴール」は、世界的なベストセラーとなりました。
その後、これらのアイディアをヒントに、様々なアイディアが発表されました。CRPを先に行う方法、MRPとスケジューラを連携する方法、MRPとCRPを融合するような方法、その他独自のアルゴリズムなどなど。この時代に考案されたものを総称して、APSと呼ばれるようになりました。
■APS導入により期待できる導入効果
APSの導入により、次の導入効果が期待できます。
APSを導入すると、工程と工程がシンクロするようになります。
前工程が完了してから、次の工程までの待ち時間が減るのです。
生産リードタイムの中身は、作業時間と待ち時間です。待ち時間の、生産リードタイムに占める割合は、平均的な日本の製造業で80%くらいだと言われています。この待ち時間が半分になるだけで、大きな効果が出ます。
具体的な指標で見ますと、
・リードタイムの短縮
・在庫の削減
・在庫回転日数の低減
に表れます。
違う指標のようですが、すべて同じことを示しています。
生産量が変化せずに、在庫が減るのですから、当然、ROA(総資産利益率)は良くなります。製造業にとってROAは、銀行の利率のようなものですから、良くなれば投資家は喜びます。
また、リードタイムが短くなれば、短納期でも間に合う場合が増えます。自然に納期遵守率が向上します。そして、納期を遵守していると、無理な割込みや調整をする場面が減りますから、計画・管理業務の負荷も下がります。
■APSを有効に活用するには
APSを有効に活用するには、
・リードタイムのムダを見抜いて改善する力
が必要です。
リードタイムには情報のリードタイムと、モノづくりのリードタイムがあります。
情報のリードタイムは、お客様や後工程からの情報が届いてから、その情報が処理されて計画を変更するまでの時間です。
メールによる伝言ゲームや、計画変更が簡単にできないと、情報リードタイムは長くなります。動き出しが遅くなるのです。
情報のリードタイムを削るには、
・情報伝達を早くする
・共有する仕組みを作る
・伝達情報に応じて適切な再計画を速く行う
という方法があります。
モノづくりのリードタイムは、部品や原料が入ってきてから、製品になってお客様の手に渡るまでの時間です。
作業に必要な時間も含まれますが、大部分は工程と工程の間で仕掛在庫として保存されいている時間です。
同じものをまとめて効率よく作ったり、前後工程の変化の影響を緩衝してくれる効果を期待して、在庫を多く持つと、リードタイムは長くなります。
モノづくりのリードタイムを削るには、仕掛かり在庫時間を削る必要があります。
仕掛かり在庫時間を削るには、
・在庫を減らす(適切な安全在庫量設定)
・ロットサイズを小さくする
という方法があります。
このようにリードタイムのムダを見抜き、改善することで、APSを有効に活用することができます。
リードタイムのムダを見抜くには、進捗や在庫などの情報を見える化しておくことが必須です。
情報の見える化を行う場合には、ITを活用するのがよいでしょう。
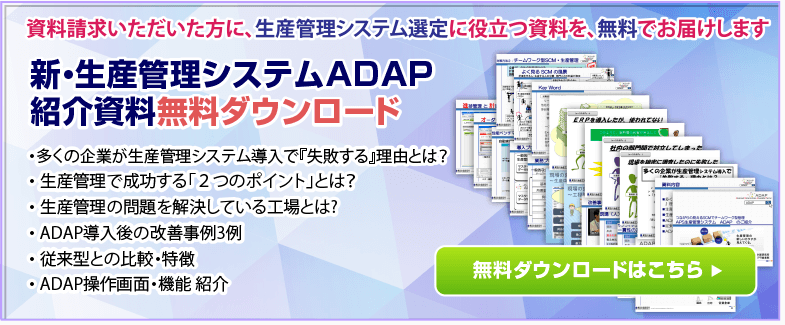
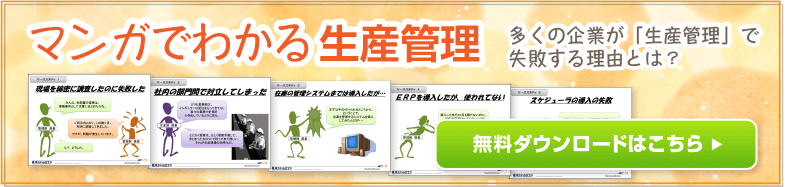
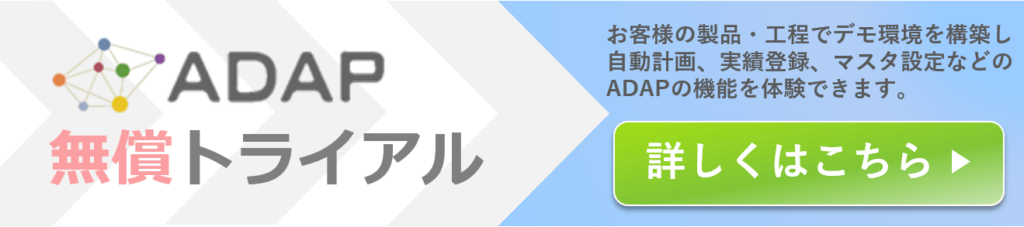