20世紀初頭にテーラーは、生産現場の標準作業と標準時間を定め、標準時間を基準にした出来高払い制とする、「科学的管理法」を提唱しました。 これが IE(アイ・イー=インダストリアル・エンジニアリング)の起源だと言われています。
最も効率の良い標準作業を定める際に行う「動作研究」と「時間研究」には、生産性改善の視点の宝庫です。このため、IEは生産性改善の技術として普及しました。
IE手法による改善は、主に現場の作業に適用されてきましたが、事務作業や管理業務にも応用できるものだと思います。 IEの考え方は、業務改善にシステムを利用する場合の要件定義に役立つアイディアの宝庫です。
ここでは、代表的なIE手法の考え方を「改善の視点」として「主体作業と不随作業」と「ECRS」の2つを取り上げ、システム化への応用を紹介していきます。
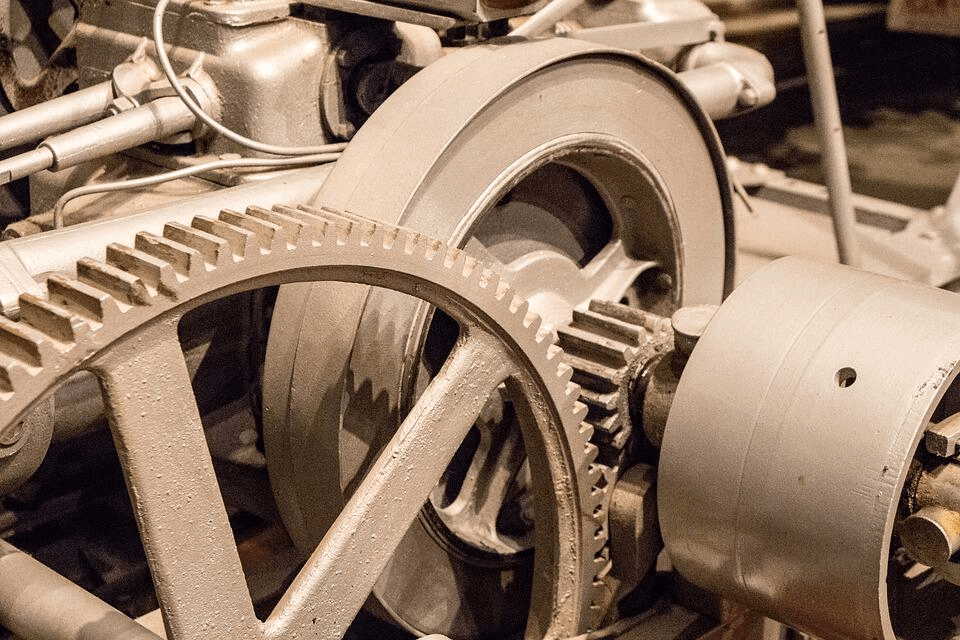
改善の視点 その1 「主体作業と不随作業」
「改善の視点」その1として、「主体作業と不随作業」という見方を紹介します。
「主体作業と不随作業」とは
どんな作業であれ、その作業の目的があります。 その目的を達成するための核心となる作業のことを「主体作業」と言います。 反対に、必要ではあるけれども、直に目的達成につながらない作業のことを「不随作業」と言い、区別します。
組立作業では、部品の位置合わせや、ビスを締める作業が主体作業です。 主体作業は、付加価値が上がっている瞬間という見方もできます。 一方、部品を作業スペースまで運んだり、段ボール箱を開けて取り出したり、ビスの数を数えたりするような作業は不随作業です。
そして、改善の基本手筋は、不随作業を減らすようにすることです。 人はどうしても主体作業に意識が向いてしまいますが、意識して不随作業に注意を向けます。 これは、主体作業のスピードを上げたり、自動化したりするより、不随作業のほうが簡単で安価に改善できる場合が多いからです。
生産計画の立案を「主体作業と不随作業」という視点で見る
この視点で生産計画を立案する業務を見てみましょう。 生産計画をたてる作業を動作分析のように分解してみると、次のようになります。 (注:動作分析もIE手法です)
① 顧客(後工程)からの注文を確認する
② 在庫を確認する
③ 不足分と余裕と現場の事情を考えて、計画を決める
④ 決めた計画を帳票に記入して現場へ送る
⑤ 必要な部品の数を算出する
⑥ 部品の在庫を確認する
⑦ 不足分と余裕を考えて、届けてほしい部品の数を決める
⑧ 決めた数を注文書に記入して部品メーカー(前工程)へ送る
このうち、主体作業は③の計画を考えて決めるところと、⑦の部品の数を決めるところだけで、残りはすべて不随作業です。
実際に作業にかかっている時間は、どうでしょうか。 主体作業は、「決める」という脳の中の作業です。 状況確認が終わってからの決定ですから、現場のことをよくわかっているベテランなら、直観的に決められる場合が多いでしょう。 時間の多くは不随作業に使われていることに気付くでしょう。
生産計画の立案における改善ポイント
スケジュラーや、MRPのようなシステムは、あなたに代わって計画を決めてくれたり、必要な部品の数を決めてくれたりします。 これらを使えば、あなたの仕事は減るでしょうか?
たいていの場合、大して変わりません。 あなたは、相変わらず顧客の注文を確認したり、在庫を確認したりして、そのデータをシステムに教えてやらなければならず、システムが決めた計画や部品の数を誰かに伝えるために指示書や注文書を作って送らなければなりません。
しかも、システムはあなたの気に入るような決定をするとは限りません。 システムは、段取りコストを最小にするとか、在庫を最小にするとか、何かを最適にするための決定は、あなたよりもスマートにこなすことができます。 だが、「少々無理をしても今回は特別にこの注文を優先させるべきだ」とか、「来週に備えて在庫を増やしておいたほうが良さそうだ」といった判断は、あなたの指示なしにはできません。 「何を最適にすべきか」は、時と場合と状況によって変化します。 「何を最適にすべきか」を決めることは、「どうやって最適にするか」を決めるよりも難しく重要です。
反対にシステムがあなたに代わって 顧客の注文と在庫を調べて、いつ・何が・いくつ 足りないと教えてくれたらどうでしょうか。 あなたが、ここで作ると決めたら、それに必要な部品数と在庫を比較して、足りない分を注文してくれるシステムはどうでしょうか。 あなたの仕事は随分と楽になるのではないでしょうか。
主体作業にフォーカスした改善よりも、不随作業を改善するほうが簡単で効果が大きくなります。
改善の視点 その2 「ECRS」
「改善の視点」その2として、「ECRS」について紹介します。
「ECRS」とは
ECRSは、E=Eliminate(削除)・C=Combine(結合)・R=Replace(入替)・S=Simplify(単純化)の頭文字を並べたものです。
ECRSは、業務を改善するときに、検討すべき優先順位を表しています。 この優先順位に従って検討することで、より効果の大きい改善に結びつくことを示しています。
最初に考えるべきは E=Eliminate(削除)。 その仕事を「なくすこと」ができないか、 あるいは「やらなくて済む」ようにできないか、と検討することです。
それができそうになければ、次に C=Combine(結合)。 なにか、他の仕事と組み合わせて、一緒に行うことはできないか、を検討します。
そして、R=Replace(入替)。 べつの仕事と順序を変えたり、場所を変えたりしたら、やり易くなるのではないかと、考えます。
最後に、S=Simplify(単純化)。 その仕事をもっと簡単にやる方法はないか、と考えます。 治具や装置、ロボットを使って自動化することも、Simplify の方法としては悪くありません。 予算が認められるかどうかは別になりますが。
生産管理の手順を「ECRS」という視点で見る
生産管理のよくあるパターンである、つぎのような手順を事例に、考えてみましょう。
① 【営業】顧客からの注文を受け付ける
② 【営業】受け付けた注文を週次で集計する
③ 【営業】先週の集計との差を分析する
④ 【営業】集計結果と、分析結果を製造へ提出する
⑤ 【製造】差異分析結果をもとに、生産計画を変更する
⑥ 【営業】計画結果を見て、顧客に納期を回答する
⑦ 【製造】計画に従って生産する
改善を意識してこの記事を読んでいる読者には、ムダの多い手順に見えると思えるかもしれません。 しかし、実際にあった事例からピックアップしています。 過去のいきさつから、こんな手順が定着していたのです。 「変更を、毎日五月雨式に受け取るのは大変だ」とか、「どう変わったのかわかりやすく教えて欲しい」とかの、「誰か」の要求が積もり積もった結果です。
解説するまでもなく、②③などすっ飛ばして、新しい注文を製造から見えるところに都度書き込めば、必要な情報は伝わります。 手間をかけて、情報の伝達を遅くしているだけです。 単純化(S)が必要になりそうなのは、⑤の生産計画を変更する方法くらいです。 先週との差ではなく、今の計画と注文のギャップから計画を変更できる仕組みを作れば、楽になりそうです。
なぜ「ECRS」という順序なのか
なぜECRSの順番なのでしょうか。 直観的に説明すると「やらなくてよいことを、効率的に行う」愚を回避したいためです。
ですが、そのことをよくわかっているつもりでも、人はなぜか Simplify を優先して思考する傾向が強くなります。 Eliminateなど、対象外だと考えがちです。
その仕事をしないで、本当に何も困らないのかを確認するのは、思いのほか難しそうです。 大きな組織で業務を分担している場合は特にそうかもしれません。 そして、「あなたが行っている仕事は、本当はやらなくてよいものだったのです」と言うのは辛いでしょう。 言われるのはもっと辛く、自覚するのはさらに辛いことです。 そんな厄介なことは、本能的に避けてしまいます。 「その仕事は、本当に必要なことですか?」などと不躾に質問するコンサルタントとは、口も利きたくないでしょう。
「ECRS」を要件定義に適用するということ
生産管理をシステム化するときの「要件定義」では、ECRSのアイディアが全く活かされないケースが多く見受けられます。
「要件定義」のコンサルは、先の例のような業務手順を、隅から隅まで、見栄えの良いチャートに書き出します。 システム会社のSEは、全部の要件を満たすシステムを開発するための金額を見積ります。 ヒアリング対象の顧客は、自分の言ったことがすべて網羅されているので満足してしまうのです。
ECRSなど、もってのほかなのです。 コンサルはヒアリング対象の顧客から嫌われるリスクがあるし、システム会社の見積金額は安くなってしまいます。
結果、高額であるにもかかわらず、改善効果の少ないシステムが出来上がるのです。
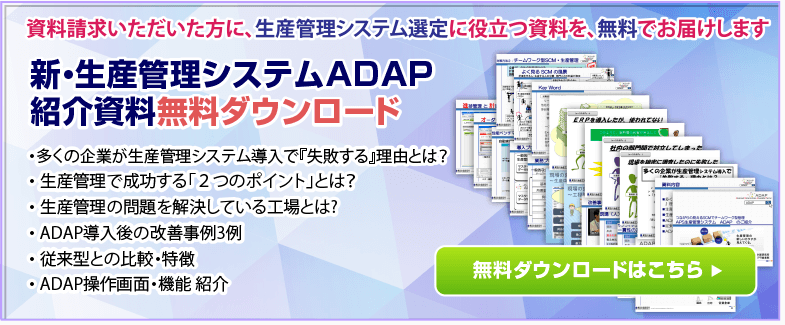
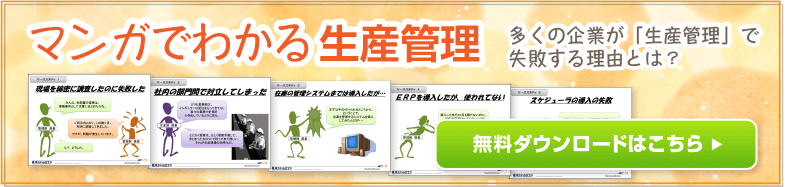
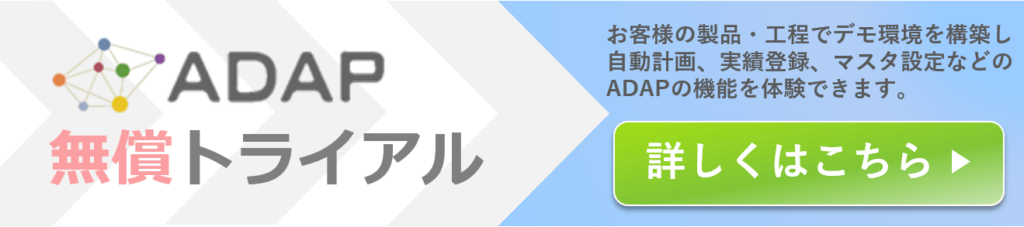