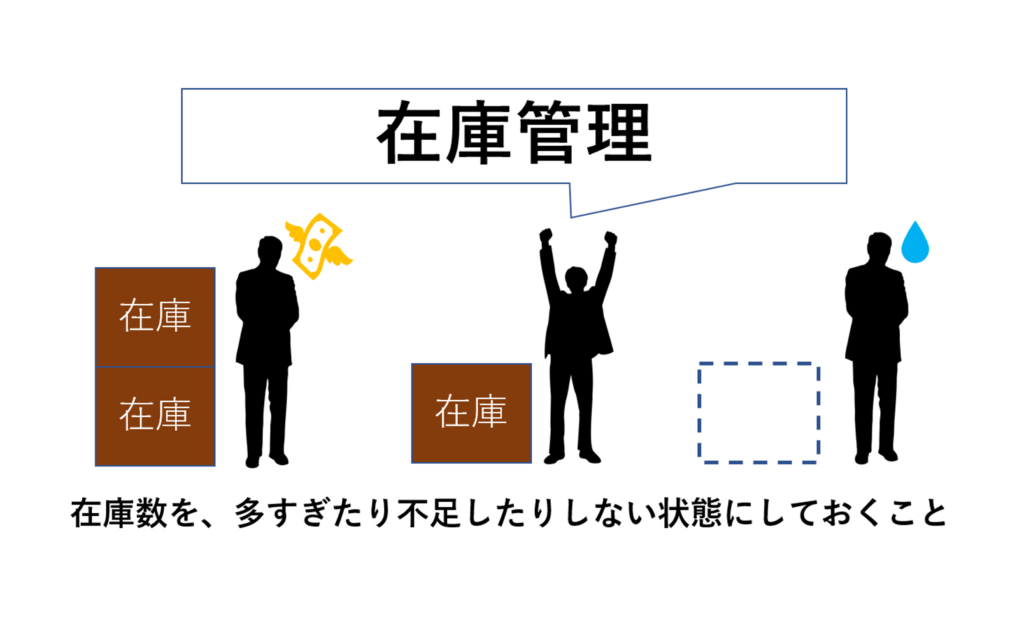
在庫管理とは
在庫管理とは、原材料や中間品、完成品など全ての品目について、在庫の数を、多すぎたり、不足したりしない状態にしておくことです。
日本産業規格 JISの生産管理用語では、在庫管理とは、「必要な資材を,必要なときに,必要な量を,必要な場所へ供給できるように,各種品目の在庫を好ましい水準に維持するための諸活動。」と定義されています。
「資材」とは、原材料や部品、仕掛品、中間品、包材、完成品(製品)など、すべての品目の総称のことです。
「在庫を好ましい水準に維持する」とは、在庫の数量を、多すぎたり、不足したりしないようにしておくという意味です。
在庫管理は、小売業や製造業、物流業などで行われますが、ここでは、製造業での在庫管理について、重要な理由・在庫管理のやり方・改善のステップをご紹介します。
在庫管理が重要である理由
製造業において在庫管理が重要である理由は、主に2点あります。
1. 在庫管理で利益を向上できる
「在庫の数を好ましい水準に維持する」ことは、製造業の利益に直結します。
在庫の不足は、目先の営業機会の損失はもちろん、顧客の信頼を失うことで将来的な機会損失の要因となります。
在庫が多すぎるということは、余分な在庫の生産にコストをかけているということです。在庫の廃棄は、そのままお金を捨てていることになります。捨てるよりかはと、安売りすることもあるでしょう。在庫を保管できる場合も、キャッシュフローには悪影響を及ぼします。在庫の維持や、倉庫のスペースの維持にもコストがかかります。また、数値には現れにくいですが、不要な在庫を作るためにリソースを割き、本当に必要な生産に悪影響が出ることも多いです。
適切な在庫管理により、製造業の利益は向上させることができます。
2. 在庫管理で従業員の働き方が改善される
在庫管理により適切な在庫数を維持することは、実は、従業員の働き方の改善にもつながります。
在庫が不足すると、不足分をカバーするためにあちこちで調整や残業を行う必要があります。そうすると、従業員は疲弊し、責任者探しで部門同士の仲も悪くなります。在庫が多すぎると、作業スペースは狭くなり、日々のピッキングや維持管理の労力は増えてしまいます。
人手不足の昨今、適切な在庫管理で従業員の負荷を軽減し、明るい職場を作ることは、企業にとって重要なポイントと言えます。
在庫管理のやり方と改善のステップ
はじめに、在庫管理のレベルと在庫管理のやり方をご紹介し、その後、現場に合わせた改善のステップをご紹介します。
在庫管理のレベルと在庫管理のやり方
在庫管理の定義を忠実に実現するために、具体的に何をすればよいのかを、当たり前のことからレベル順に説明すると、以下の6つにわかれます。
レベル0:今、在庫がいくつあるのか数える。
レベル1:在庫の増加と減少の実績を都度把握して「今在庫がいくつあるはずなのか」を常時把握する
レベル2:在庫が減少する計画を把握して、将来の在庫推移を把握する
レベル3:在庫がマイナスになる前に在庫を増やす手配をして、マイナスにならないようにする
レベル4:レベル3の生産計画に、必要な資材を前工程に要求する
レベル5:完成品の需要予測を追加する
レベル6:制御できないバラツキに備える
レベルごとに実際のやり方をご説明します。レベルが上がったら、低いレベルの活動をしなくても良いと言う訳ではなく、前のレベルの活動も継続して、その上に積み重ねていく必要があります。
レベル0:今、在庫がいくつあるのか数える
在庫の量を知りたくなった時に、数えて量を把握します。これが最低限の在庫管理です。「棚卸し」とも言われます。
レベル1:在庫の増加と減少の実績を都度把握して「今在庫がいくつあるはずなのか」を常時把握する
生産などの実績を元に、在庫を算出できるようにします。これで、数えに行かなくても、いつでも在庫の量がわかるようになります。それでも時々数えに行って(レベル0は継続)、誤差が出てないか確認して、修正をします。
誤差が大きい場合には、増減の実績把握に問題があるはずです。原因を突き止めて改善してください。
レベル2:在庫が減少する計画を把握して、将来の在庫推移を把握する
製品であればお客様の注文に基づく出荷計画を減少する計画とします。中間品や部品・材料であれば、それを使用する後工程からの要求を取りまとめて、減少する計画としてください。
レベル1で把握している「今の在庫量」から、在庫の推移が把握できるようになります。
このレベルでは確定情報だけを扱い、予測や見込み、「いざ」というときの予備については、いったん考えないようにします。
レベル3:在庫がマイナスになる前に在庫を増やす手配をして、マイナスにならないようにする
レベル2の結果、在庫が不足する時がわかります。それ以前に、在庫を増やすように手配します。
購入している材料や部品なら、仕入先に発注します。発注しても、即時に在庫を増やせるわけではありません。手配してから納入されるまでの時間差(リードタイム)を考慮して、手配するタイミングを決めてください。
中間品や完成品ならば、生産を計画して製造部門に指示してください。生産を計画する場合には、工程の生産能力・歩留まり・ロット
サイズ制約を考慮して、生産日程を決めてください。
レベル4:レベル3の生産計画に、必要な資材を前工程に要求する
レベル3で生産計画を立てた場合、その計画で必要となる資材を前工程に要求してください。この要求が、レベル2の要求につながって、連鎖します。
その結果、完成品の出荷計画から、すべての完成品と中間品の生産と、購入する材料や部品の調達の計画を決めることができるようになります。
―――――――――――――――――――――――――――――――――――――――――
レベル4で、確定情報に基づく、生産管理の仕組みが整います。
次のステップから、未確定情報を取り込んでいきましょう。
―――――――――――――――――――――――――――――――――――――――――
レベル5:完成品の需要予測を追加する
なるべく予測精度の高い情報を使いましょう。出荷先から内示情報をもらっている場合には、その内示情報を使うのが良いでしょう。内示情報の精度を検証して、精度不足の場合には補正します。
具体的な方法については、別途セミナーで解説しておりますので、興味がある方はご連絡ください。
レベル6:制御できないバラツキに備える
完成品の需要予測ももちろんバラツキます。生産も、計画と実績にブレがでたり、資材の消費量にバラつきがでたりします。バラツキが少ないに越したことはないのですが、制御できないバラツキが残る場合があります。
そのバラツキに備えて、各資材の安全在庫量を設定して、いつもその安全在庫量を下回らないように計画・管理してください。
―――――――――――――――――――――――――――――――――――――――――
以上で、JISで定義されている在庫管理の「諸活動」として必要なものが揃いました。
お気づきでしょうか? 結果、生産管理の機能がすべて揃ってしまいました。JISの定義によると、在庫管理だけを生産管理から切り離して行うことはできないというわけです。
「在庫管理のレベルと在庫管理のやり方」でご紹介したレベルは、必ずしも実際の活動を進める手順ではありません。考え方として、理解しやすい順(目の前の現実 →確定値から計算できる未来 →ある程度の精度で予測できる未来 →制御できないバラツキを含む未来)にレベル設定しました。
現在生産しているものについて、いきなり需要予測や安全在庫を取っ払うのは現実的ではありません。ただし、確定情報だけでどこまで整理できるのかを、論理的に確認したほうが良いと思います。その上に、予測や安全を載せていくという考え方がおすすめです。
安全在庫の設定の注意点
レベル6の、安全在庫の量を決めるためには、正規分布を使った統計的手法を用います。この手法だけを取り上げて、在庫管理の理論としている解説も多く存在します。しかし、レベル0~5のまでの積み上げをせずに、いきなりレベル6だけにこの手法を適用するのは誤りです。
なぜなら、正規分布は制御できない誤差に当てはまる分布だからです。
1809年に数学者のオイラーは制御できない誤差が、つぎの次の3つの条件から演繹的に正規分布を導き出しました。
1.大きさの等しい正と負の誤差は等しい確率で生じる。
2.小さな誤差は、大きな誤差よりも起こりやすい。
3.ある限界値より大きな誤差は、実際上起こらない。
確定値と、ある程度の精度で予測できる値による変動まで含めてしまっては、上記の条件に当てはまらないので、正規分布にはならないのです。
この記事を参考に、ぜひ一度、貴社の在庫管理を見直してみてください。全員で確認出来る在庫表があると便利です。もっと利益を上げ、従業員みなが納得して働く職場をつくるヒントになるでしょう。
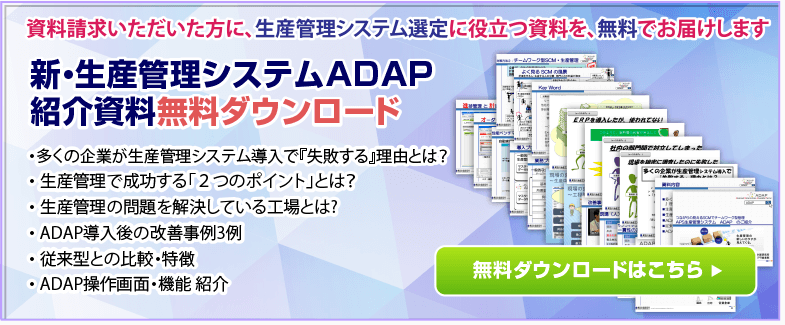
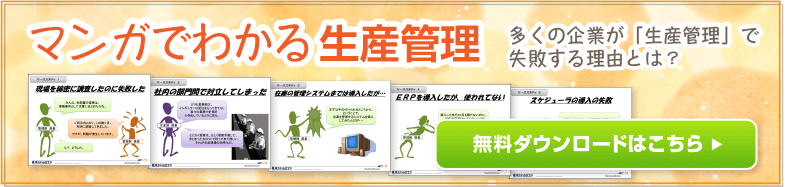
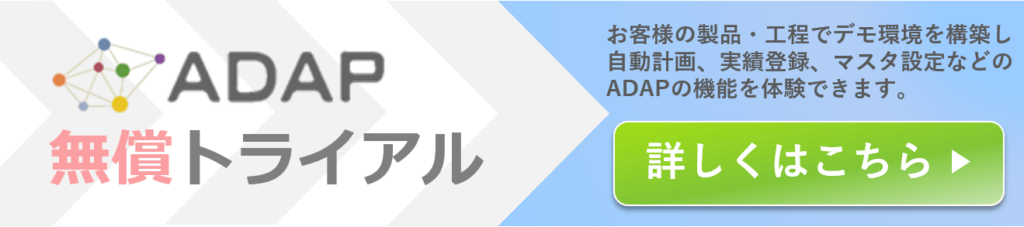