■MRPとは
MRP(Material Requirements Planning:資材所要量計画)とは、独立需要品目(*1)の需要とBOM(Bill Of Materials:部品表)をもとに、従属需要品目(*2)の所要量を計算する手法です。所要量をもとに在庫・発注残・ロットサイズを考慮し、リードタイムを仮定して、生産計画や調達計画を決定します。
将来の需要に必要な量だけを計画することから、在庫が適正化される画期的な手法として1960年代から普及しました。現在でも多くの生産管理システムにおいてこのロジックが採用されています。
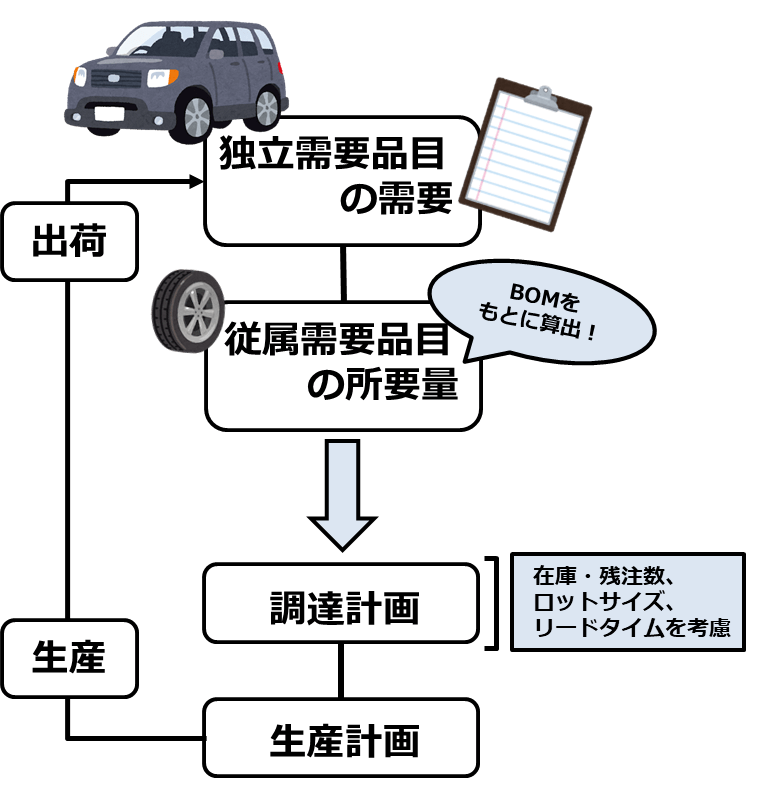
________________________
*1 受注または予測に基づいて、その必要時期または必要量を決定する品目。
最終製品、サービスパーツなど。
*2 独立需要品目にぶら下がっており、
需要が独立需要品目または上位品目の需要から算定される品目。
■MRPはプッシュ型?
しかし、実際の運用ではMRPを用いた生産管理では、トヨタのカンバン方式と比べて多くの在庫を必要としてしまいます。1990年にマサチューセッツ工科大学の研究者が出版した著書で、少ない在庫で運用する「リーン生産方式」としてカンバン方式が紹介されました。
そのなかで、カンバン方式はプル型(後工程引き取り方式)だから少ない在庫で運営できると説明されました。
これに対し、MRPはプッシュ型(計画に基づいて押し出す方式)だから、在庫が増えてしまうというのが定説になってしまいました。しかし、前述したように、MRPは将来の需要から逆算して計画しています。それなのになぜ、プッシュ型と言われるようになってしまったのでしょうか?
■MRPがプッシュ型と言われてしまう理由と問題点
原因は、MRPが抱える2つの欠点にあります。
① 計算に時間がかかる
当時のコンピュータ能力が低かったため、計算には長い時間がかかりました。そのため、月1回や週1回しか実行できませんでした。
特にメモリが少なかったので、アルゴリズムはメモリを消費しないことを重視して設計されました。現代のMRPでもこのアルゴリズムが引き継がれているものが多く、MRP計算に時間がかかるものが散見されます。
② 設備の負荷を考慮できない
同様に、当時のコンピュータ能力では、設備の負荷を考慮した計画を立てることができませんでした。設備の負荷を考慮した山崩しはMRP計算の後で別途実施していました。このプロセスは山積み、山崩しと呼ばれます。
山崩しをしたときに、前工程の計画を追い越さないようにMRPのリードタイムを長めに設定しておく必要がありました。
(詳しい解説はこちら:「MRPはなぜ『プッシュ型』と呼ばれているのか」)
リードタイムが長く、月(週)に1回しか計画しないため、遠い未来の販売予測による計画しか立てられず、直近の受注による計画は立てられません。その結果、「プッシュ型」と言われるようになってしまったのです。
■MRPからMRPⅡ、ERPへの発展
その後、MRPは2つの方向で改良が加えられます。
1つは、資源負荷を考慮するために考えられたクローズドループMRPです。MRP計算のあとで山崩し計算を行い、成立しない場合はリードタイムを長くしてMRPをやり直すというものです。しかし、ただでさえ時間のかかるMRP計算を何度も繰り返すのは、現実的でなくあまり普及しませんでした。
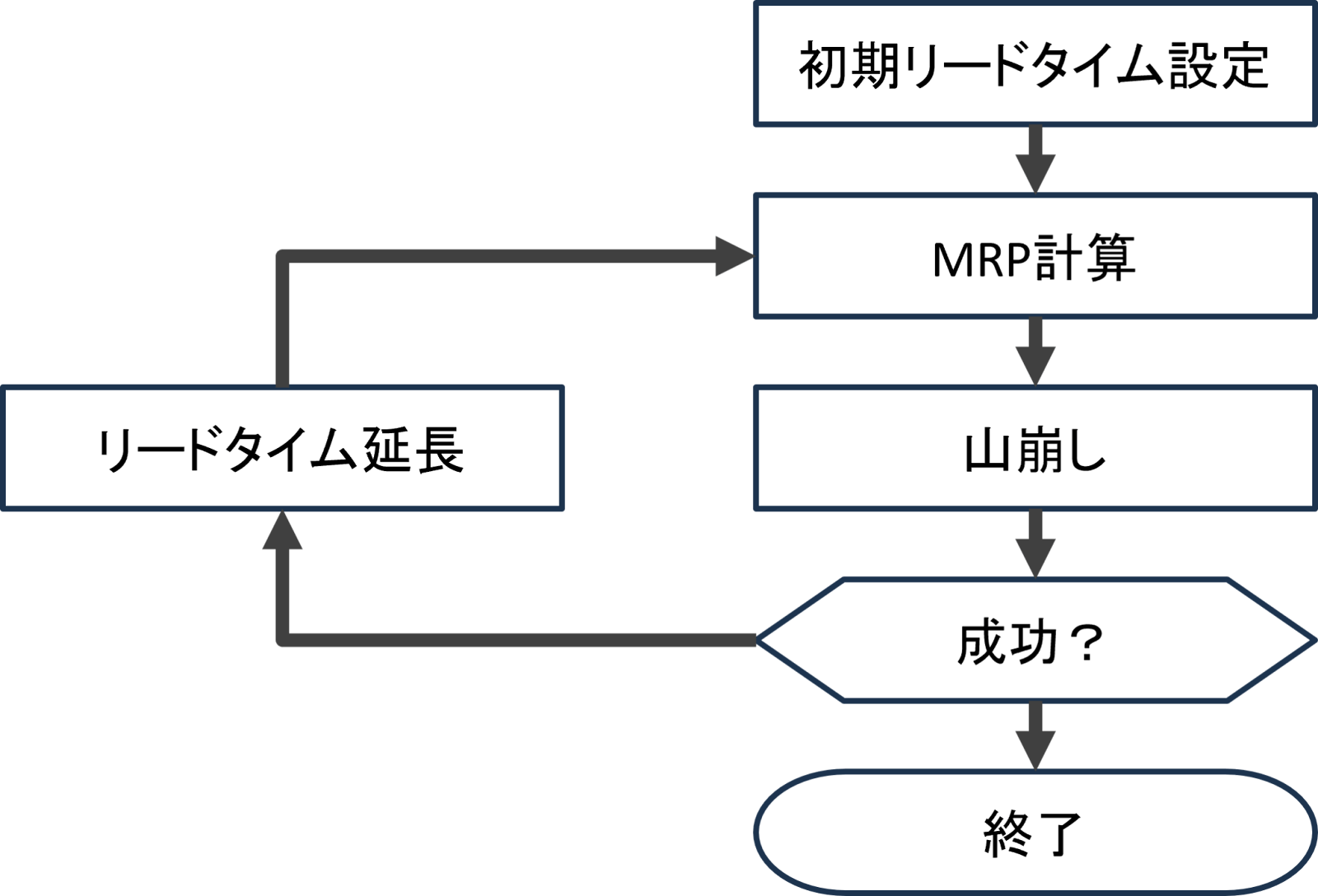
もう1つの方向は、会計や財務を含めた会社全ての資源を管理するMRPⅡ(Manufacturing Resource Planning:生産資源計画)です。これはやがて、ERPへと発展していくことになります。
■TOC(制約理論)の出現からAPSへの発展
1980年代の中ごろ、物理学者ゴールドラット博士によって、TOC(Tehory Of Constraints:制約の理論)が発表されました。ボトルネック工程を制約として、ボトルネック工程の計画に全体をシンクロさせるという新しいアプローチでした。ビジネス小説として出版された「ザ・ゴール」は世界中でベストセラーになりました。
山積み、山崩しによりリードタイムが長くなってしまう問題が、根本的に解決出来ずにいたMRPシステムにとって、TOCはまさに目から鱗の新発想でした。
その後、この理論の研究が進み、所要量計算と資源負荷計画を同期的に計画する手法へと発展しました。日本ではこの手法はAPS(Advanced Planning and Scheduling)と呼ばれています。最新のAPSシステムは、TOCを発展させた考え方を取り入れて、現在のコンピューターの性能をフルに活かせるアルゴリズムで開発されています。プル型生産よりも在庫が増えてしまう問題を解消することが出来ています。
■まとめ
大量に製品在庫を持ち、在庫を販売していた時代に、未来の販売計画に基づいた生産計画・調達計画をたてる手法としてMRPが登場しました。当時としては、納期を遵守しつつ、在庫を削減できる画期的な手法でした。
初期のMRPは、当時のコンピューター性能の制約により、設備負荷を考慮することができませんでした。その結果、実現性の保証、リードタイム短縮、在庫削減の効果には限界がありました。
時代が、大量生産から多品種少量生産へと移行する中、更なる改善が求められました。その要求に応えるべく、改良の努力が重ねられてきました。その中でも、TOCのアイディアが、革新的な影響を与えました。所要量計算と、資源負荷計画の同期を図る基本原理と効果が示されました。そして、最新のコンピューターの性能を活用しながら、高速APSへと発展していきました。
多くの生産管理システムでMRPが活用されていますが、いまだに所要量計算と資源負荷計算が同期していないシステムも存在しています。最新のAPSに変更することで、カンバン方式の採用が難しい現場でも、プル型生産以上の短納期。在庫削減効果が期待できます。
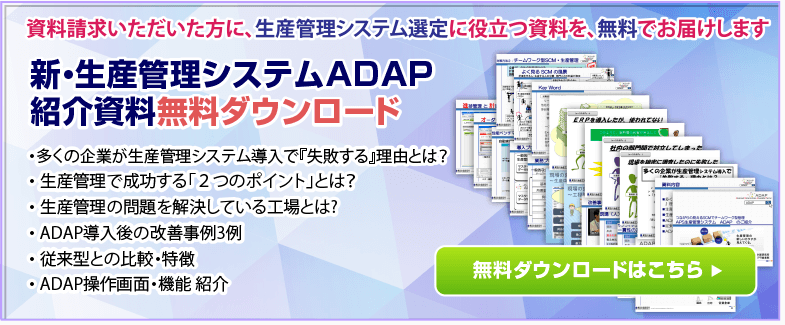
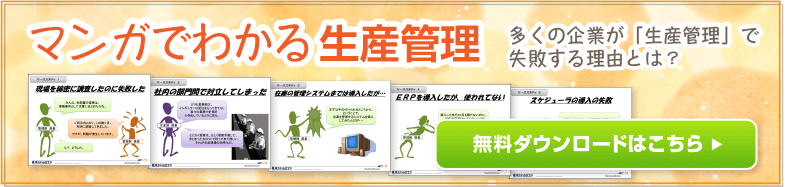
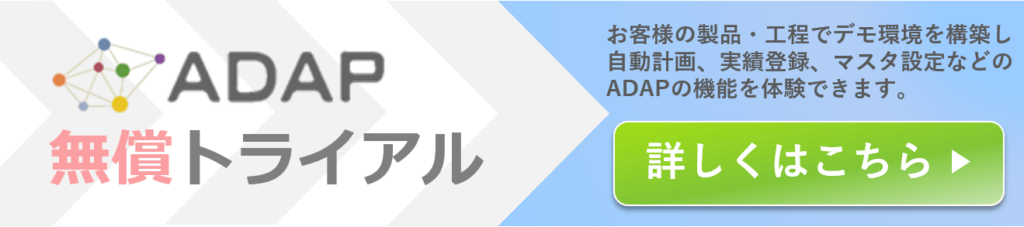