工程管理とは
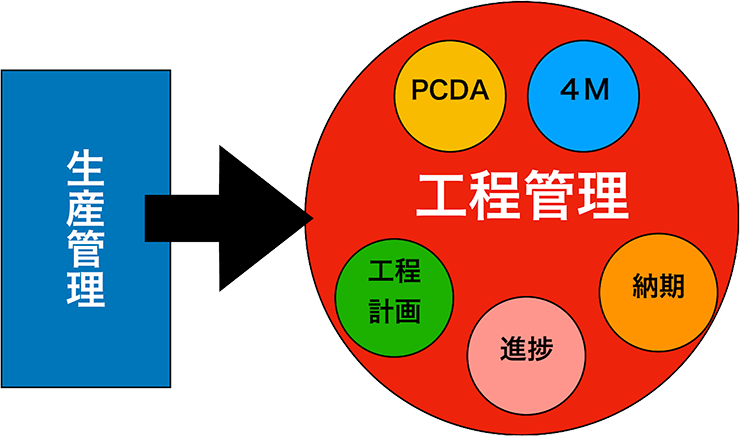
工程管理:高品質の製品を効率よく生産するために
工程管理とは、計画通りの製品を効率よく生産するために、作業者、機械設備、作業方法および材料の4つを管理・運用する活動のことです。ここでは、工程管理の手順や方法、ツールなどを解説しています。
◾️工程管理とは
製品の製造工程において、品質の良いものを効率良く作るために、製造工程を構成する4M=Man(人)・Machine(設備)・Material(モノ)・Method(方法)
を管理し運用することです。
最適な工程管理を行うことで、製造工程の ダラリ(ムダ・ムラ・ムリ)を省き効率の良い「ものづくり」ができます。
工程管理と生産管理の違い
工程管理と生産管理は混同して使われる場合がありますが、基本的には次のような違いがあります。
・生産管理:需要と供給の調整を行い、在庫量を管理しながら、生産の計画を立案、実績を把握する活動。生産の計画に当たっては、設備能力、標準作業時間、必要なリードタイムなどを考慮する。また、生産の計画を実行するのに必要な資材の手配も行う。
・工程管理:標準作業を定め、いつでも標準作業どおりの作業が実施できるように、職場を管理すること。設備の保全、作業者の教育・技能訓練、品質管理を含む。
工程とは?工程管理の4M
製造現場で使われる工程とは、最終的な製品として完成するまでの作業手順を管理単位に分解したものです。標準作業通りに作業を行うことで正しい製品が完成します。
この工程は4つの構成要素で成り立っています。
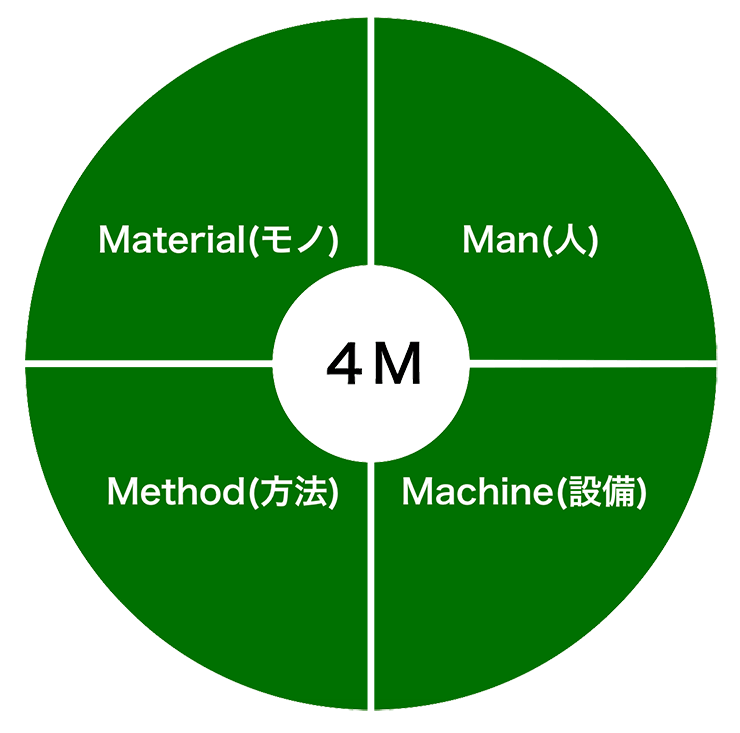
Man(人)・Machine(設備)・Material(モノ)・Method(方法)この4つのうち1つでも変化があったらそこに注意を向けることで、トラブルを未然に防ぐことができます。
◾️歴史から見る工程管理
現代の工程管理を理解する上で重要な20世紀以降の工程管理の簡単な歴史を振り返ります。
・テイラーの科学的管理法
フレデリック・テイラーが提唱したもので、生産工程における作業に含まれる動作を細かく分解して動作研究を行い、最も効率のよい動作を標準作業として定め、標準の作業者が、標準の努力で、標準作業通りに作業を実施した場合の時間を、標準時間と定めました。 標準時間を定めたことで、生産現場に「管理」の概念が確立し、計画的な生産を実施できるようになりました。
・IE:インダストリアルエンジニアリング
テイラーの動作研究などが、のちに改善の技術 IEとして発展しました。 IEの技術は製造現場をより効率的に変えてゆくための問題解決の科学的アプローチの一つです。 現状把握を目的としたいわゆる「見える化」の効果を使っています。 時間や作業を数値でまとめたり、図でまとめることによって、改善の余地を見つけるための工程管理の一つのツールです。
・トヨタ生産方式
トヨタ自動車の生み出した、工場における生産活動の運用方式で、7つのムダの削減、ジャストインタイム、標準作業時間に代表される現場主義の人が関わる改善による(ニンベンのついた)自働化を重要視した工程管理の一つの技術です。
◾️工程管理の4つの目的
工程管理の目的は、「工程計画」「進捗計画」「工数計画」「現品計画」を遂行し、生産計画に従って製造工程が正常に運営されているかを管理し納期を遵守することです。
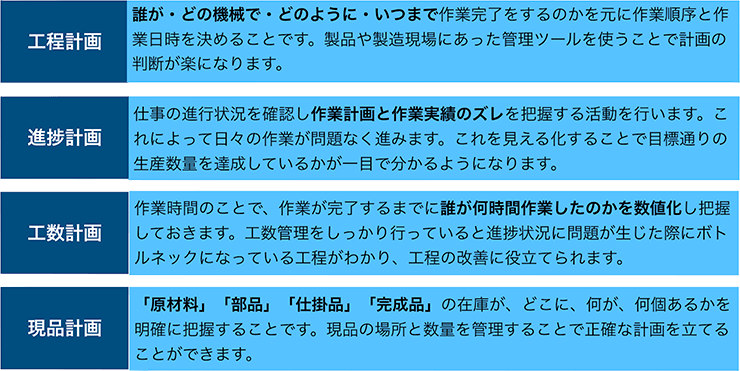
◾️工程管理のメリット
ここでは工程管理のメリットを紹介します。
コストを抑えながら生産性を高めることができます
工程管理を行うことで、無駄を見える化できるので改善点が見つけやすくなります。
改善することでボトルネック工程での作業工数を減らすことができれば、人件費の削減にもつながりコストを抑えながら生産性を高めることができます。
安定した品質を保つことで顧客から信頼されます
工程管理によって製品の生産プロセスを常にチェックすることで、製品の品質を常に一定に保つことができます。
何の作業をどのように行えば良いかを明確にすることで正しい工程・方法で作業でき、製品の品質に大きな差が生じることは少なくなります。顧客に満足してもらえる品質を保てるようになれば、結果的に企業の信頼度が向上します。
作業員のモチベーションの維持につながります
作業方法にムダがあっては生産量を増やすことができません。そのせいで作業員の残業が多くなってしまっては、現場で働く作業員のモチベーションは下がってしまいます。
工程管理によって作業のムダを省くことで、作業員のパフォーマンスを高めることができればモチベーションを維持することにつながります。
◾️工程管理の改善手法と手順
ここで説明する工程管理の改善手法であるPDCAサイクル(PDCA cycle、plan-do-check-action cycle)は、日本の製造業成長の起点となった改善手法です。
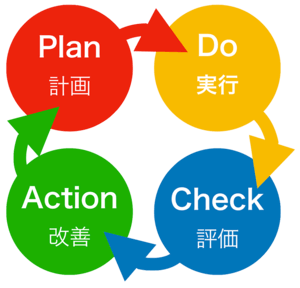
Plan(計画)
まずは、従来の実績や将来の予測などをもとに目標を決めます。目標を達成するために必要な計画を立案します。
・製品の種類や数量を決定します。
・4Mを確認します。(人・設備・モノ・方法)
・そして作業完了までの工数をもとに工程計画を行います。
Do(実行)
次に立案した計画をもとに生産を行います。
・生産がスムーズに進んでいるかを確認します。
・問題や改善点があればそれを書き出しておきます。
・生産状況の確認はできる限り数値化します。
・結果は見える化することが大切です。
Check(評価)
次に目標に対する進捗状況を確認し目標を実現できているかを確認します。
・問題点があれば原因を調べて書き出してください。
・個人的な感想や意見ではなく出来るだけ数値化した結果から評価していきます。
・改善案を出して効率の良い生産方法を考えます。
Action (改善)
評価・見直した内容をもとに、適切な処置(改善)を行ないます。
良い品質の製品やサービスを生むプロセスをレベルアップするために改善案を実行します。
それでもいい結果が出ない場合は、もう一度計画から練り直し、目指す工程が出来上がるまで改善を続けていきます。
このPDCAサイクルが正しく機能すれば、業務改善に繋がっていきます。
◾️工程管理の見える化ツール
工程管理をするためには工程表を作る必要があります。それぞれの特徴に合わせて工程を見える化することで情報の共有と業務の効率化を行えます。ここでは、代表的な工程表をご紹介します。
紙やホワイトボード
紙やホワイトボードを使用する方法なら、紙やホワイトボード、ペンがあれば問題点や改善案をすぐに記録・修正できます。特にホワイトボードは見やすく、手軽に修正できるので、進捗状況の報告や相談を口頭で行える場合、情報につながりを持たせることができて、チームワークを発揮しやすくなります。
ガントチャート
ガントチャートとは、それぞれの作業開始日と完了日までの期間をバーで示し、各作業との関係や人員、工数などの工程を視覚化する表のことで、作業の流れと進捗状況を一目で把握できるようにした棒グラフです。
複数の作業の進捗状況の全体像が把握できますが、想定外のトラブルや計画変更が頻発したときにチャートの更新に膨大な時間がかかり「今どうなっているのか」が分かりづらくなることがあります。変更が発生した場合、こまめに修正を入れることで計画通りに作業を進めることができます
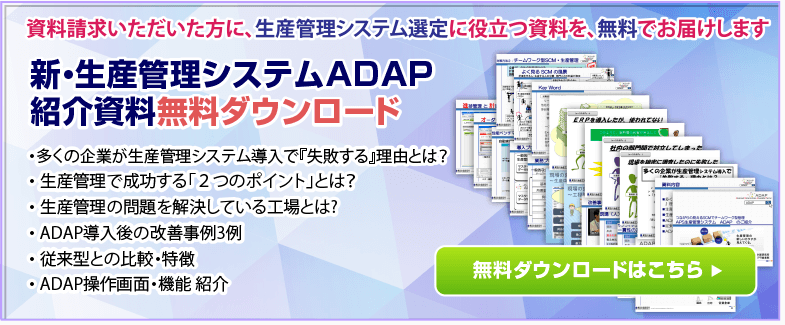
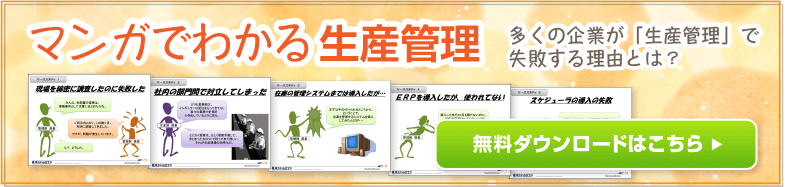
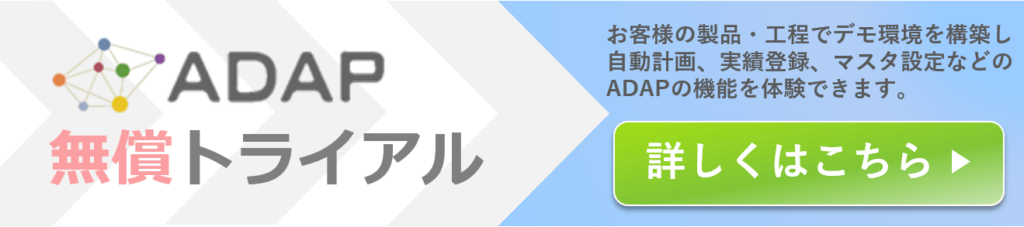