■フレキシブルな製造を実現するための生産管理システム導入
個人の消費スタイルがより細分化され、製造の現場においても、小ロットかつ短納期というマーケットの需要に対応しなければ、競合から取り残されてしまう時代になってきました。
大量の製品在庫に頼らなくとも、需要の変動に追随できて欠品の発生しない、フレキシブルな製造を実現するため、生産管理システムを導入する企業が増えています。
しかし個々の生産現場に合った生産管理システムを導入することができなければ、うまく運用できないという結果に終わってしまうことも少なくありません。
製造現場のサプライチェーンにおいては、膨大で複雑な情報を扱うため、すんなりと導入できるケースは少なく、システム導入活動そのものがなかなか進まないケースや、システムを導入したものの使ってもらえないケースなど、失敗が多いことも事実です。
利便性が高まるはずだった生産管理システム導入が、かえって従業員の工数を増やしてしまっては本末転倒です。
そこで、生産管理システム導入時によくある失敗例5つのパターンをご紹介します。
■生産管理システム導入時によくある失敗例5つのパターン
(パターン1)現状の業務要件を綿密に調査してシステム化しようとした
調達、営業、生産、流通など、各部門の業務を細かく調査し、業務要件として文章化をおこなった。
要件に沿ってシステム化しようとしたら、システム化の費用が膨大に膨れあがってしまい中断してしまった。
パッケージソフトも検討したが、どれも要件にピッタリとは当てはまらず、結局カスタマイズ費用が膨れ上がってしまう。
(パターン2)部門ごとのあるべき姿を描こうとしたが、それぞれの部門の主張がまとまらない
現状にとらわれることなく、あるべき姿を追求しようとしたのだけど、部門間の利害が対立してまとまらなかった。
営業部門は、需要予測には自信がなく、在庫の欠品を極端に嫌がります。
生産部門は、大ロット生産を希望して、折り合いをつけようとすると、在庫が今よりも増えてしまった。
物流部門は、大ロット輸送を希望してくる。
(パターン3)在庫管理システムを導入したが、その先が進まない
まずは手の付けられるところからと、在庫管理システムを導入した。
在庫量が正確に把握できるようになり、ある程度の効率化は実現できた。
しかし、ムダな在庫を削減するという本来期待していた効率化は実現されなかった。
(パターン4)ERPシステムを導入したが、使われていない
ERPを導入したものの、マスターデータのメンテナンスが滞ってしまい、現場がシステムを活用しなくなった。
しかし、ERPは原価計算も担っているため、システムを使わない訳にもいかない。
結局、今まで通りのやり方で作成した計画や実績を、システムに入力するという、管理部門の手間が増えただけで終わった。
(パターン5)生産スケジューラ導入の失敗
生産スケジューラを導入したが、思うような生産計画を得るためにはかなり工夫が必要で、かえって工数がかかってしまうようになった。
現場がスケジューラの複雑さについていけず、マスターのメンテナンスも滞り、結局1~2年で使われなくなってしまった。
■生産管理システム導入で失敗しないために
生産管理システムを導入する目的は、多品種・少量・短納期に対応するフレキシブルな製造の実現です。 なおかつ製造の効率を大幅に落とすことなく実現できなければなりません。
ですが、複雑な生産管理システムを導入したり、検討を重ねているうちに、
・生産管理システムをいかにスムーズに導入するか
・生産管理システムの導入コストをいかに下げられるか
・生産管理システムをいかに効率よく運用するか
など、
「フレキシブルな製造の実現」という目的から、いつのまにかずれていってしまいます。
ですから、生産管理システムを導入する際は、導入の目的がブレないよう、何のために生産管理システムを導入するのか。という点を確認しながら進めましょう。
また、複数の部門間での事前の調整が必要になりますので、生産管理システム導入のチームを結成すると良いでしょう。
生産管理システムを初めて導入する場合は、生産管理システム専門のコンサルタントにアドバイスを受けながら、システム導入を進めていくのも、失敗の可能性を少なくする方法です。
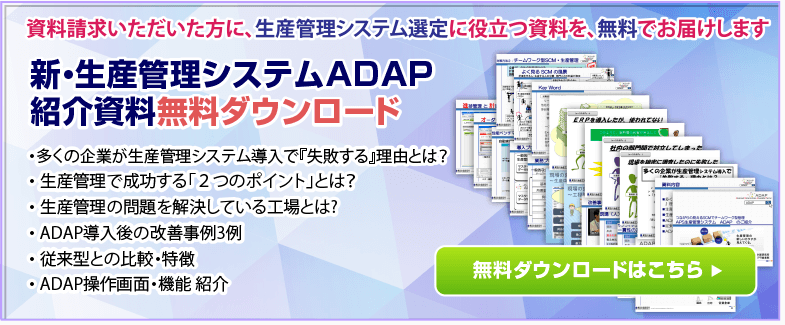
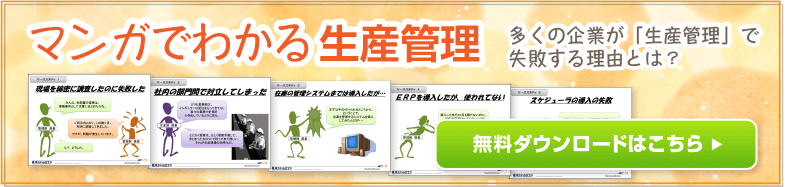
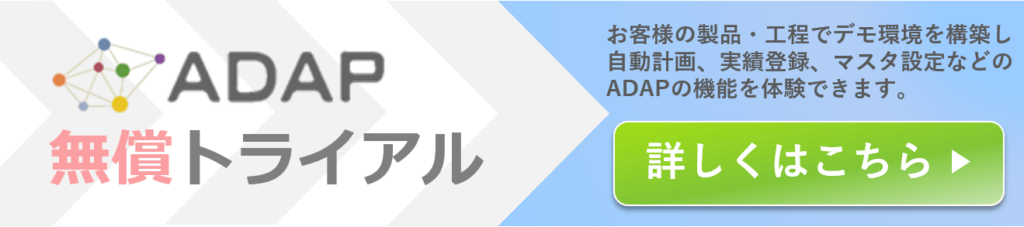