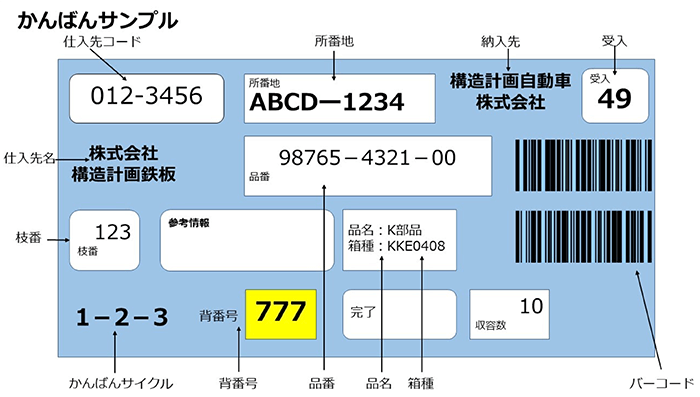
カンバン方式とは
カンバン方式とは、簡単な板切れ(かんばんのこと)を使い、難しい理論もコンピューターも使わずに、上手に生産を管理することができる、日本オリジナルの生産方式です。
カンバン方式はトヨタ自動車によって発明されました。
トヨタ自動車のジャストインタイム生産方式で使われる、工程間の流れを制御する方法です。
原理は単純で、まず後工程で部品を使用すると、前工程へかんばんを送ります。
次に、後工程からかんばんが届くと、届いたかんばんが生産指示であるため、生産して後工程の在庫を補充します。
かんばんには部品の名前と、数量が書かれています。
カンバン方式誕生のきっかけ・背景
1960年ころ、アメリカの自動車産業ではMRPを用いた生産方式が主流でした。
当時のMRPは、大型のコンピューターで計算されており、結果的に多くの在庫を持って運用されていました。
当時の生産方式を見学したトヨタ自動車の一行は、直観的に「これは、うちでは無理だ」と感じたと言います。
大型のコンピュータやMRPのシステムが高額であるだけでなく、狭い日本の工場や、手持ち資金ではアメリカのように多くの在庫を抱えることができませんでした。
まだまだ、日本は裕福な時代ではなかったからです。
トヨタ自動車の一行は、見学の帰りに立ち寄ったスーパーマーケットで、カンバン方式のヒントが得られました。
スーパーマーケットの棚に陳列されている商品を、店員が見回り、棚に空きが出ていたら補充していたのです。
スーパーマーケットの陳列方法を見て、「これでいいじゃないか」ということになりました。
カンバン方式とMRPとの違い
カンバン方式は、後工程が部品を使ったことをトリガーとして、生産を指示するため、「後工程引取り方式」とか、プル型(引張型)の生産方式であると言われています。
カンバン方式に対し、MRP(Material Requirement Planning)は、あらかじめ立てた計画に従って生産するため、プッシュ型(押出型)と言われ、プッシュ方式だから在庫が多くなると言われています。
これは、冤罪であると言えます。
MRPは未来の計画に対して、部品の必要量を計算するので、未来の計画からのPULL型であると言えます。
ところが、1960年代当時のコンピューター事情や、それに制約を受けたオリジナルのMRPのアルゴリズムのせいで、結果的に在庫を多く持つ必要があったのです。
この冤罪については、別途MRPの記事で詳細を説明し、MRPの進化系についても解説します。
ただ、残念なことに コンピューターが大きく進化した現在でも、多くのERPに組み込まれているMRPには、1960年台に開発されたオリジナルのMRPのアルゴリズムが踏襲されています。
こういったMRPをそのまま使うと、在庫が増える危険性があるので留意してください。
カンバン方式とジャストインタイムとの関係
前述したとおり、カンバン方式は、トヨタ自動車のジャストインタイム方式のなかの1要素です。
ジャストインタイムは、JIT、トヨタ生産方式、TPS、リーン生産方式とも呼ばれています。
ジャストインタイム方式とは、製造現場のムダを徹底的になくし、生産を平準化させることを総合的に実現する方式です。
生産現場7つのムダとして、
①作りすぎのムダ
②手持ちのムダ
③運搬のムダ
④加工そのもののムダ
⑤在庫のムダ
⑥動作のムダ
⑦不良のムダ
を戒めています。
また、設備には、不良を検知したら停止して異常を知らせる機能を付けることを「自働化」(ニンベンがついているところがポイント)と言い、これにより人が張り付いていなくても良い仕組みを求めています。
ムダの徹底排除や、平準化を行わずに、かんばんだけ真似をすると、たいてい痛い目に合うので注意をしたほうが良いでしょう。
カンバン方式をトライして挫折した現場を、いくつも見たことがあります。
カンバン方式をやるときには、JIT生産方式丸ごと導入したほうが良いでしょう。
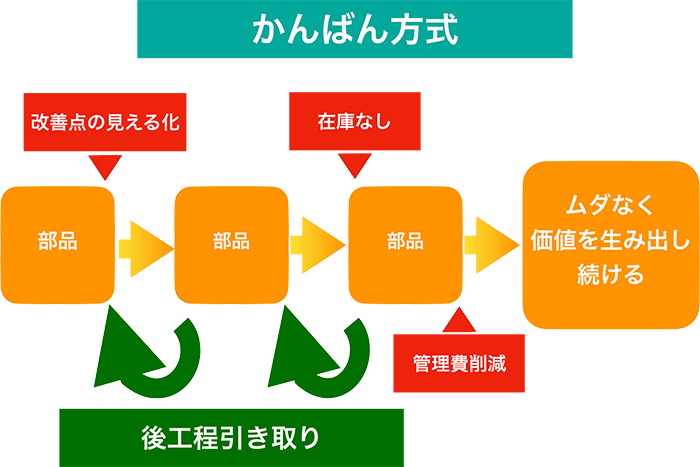
かんばんの種類と使い方
かんばんの種類と使い方ですが、要は、前工程に情報が届けば良いのですから、種類も使い方も自由で構いません。
最近は、物理的に板切れを運ぶよりもネットで情報を飛ばしたほうが良いと、「電子かんばん」なるものも登場しています。
カンバン方式だからといって、アナログにこだわる必要はありません。
アナログ方式では、かんばんを上手に流通させるために、2種類のかんばんを使い、以下の手順で情報の伝達と、現物の供給を行います。
① 後工程は、部品が欲しくなると「引取りかんばん」を持って在庫置き場へ行く。
② 現場に張り付いている「生産指示かんばん」を外して、前工程へ送る。
③ 持ってきた「引取りかんばん」を現物に張り付けて持ち帰る。
④ 前工程は、「生産指示かんばん」を受け取ったら、生産して現物に「生産指示かんばん」を張り付けて、在庫置き場へ補充する。
かんばんを受け取った前工程は、決められたリードタイム以内に、在庫置き場へ供給しなければなりません。
遅延すると、在庫が欠品する可能性が高くなるように、かんばんの枚数とリードタイムが設定されています。
かんばんを種類と納期別に整理して、見えるように置いておきます。
整理された看板を見ながら、次に何を作るかを決めます。これを差立て板と言います。
かんばんが、わかりやすい計画ボードに変身するところに、工夫を感じられます。
カンバン方式のメリット
カンバン方式は、安価でシンプルな仕組みで、サプライチェーンを管理出来てしまうところが、最大の魅力です。
計画を立てる必要も、実績を管理する必要もありません。それでいて、MRPを使っていた工場よりも、少ない在庫で上手に生産を回せていたのだから、すごい方式です。
1980年代に日本の工場を調査に来たマサチューセッツ工科大学の先生方は、さぞ驚いたことでしょう。
この話は、後に「リーン生産方式」と題した本で、発表しています。
カンバン方式のデメリット
カンバン方式のデメリットは、以下の3点になります。
・情報の伝達が遅く、未来を見通せない
在庫を使ったという、過去の実績が指示のトリガーになるので、未来の計画を見通した計画よりも情報が伝達されるタイミングが遅いです。
また、生産した在庫が、いつ使わるれのかは、分かりません。
そのため、実際に使われる時期を見越して、納期を調整するなどということが出来ません。
・かんばんの枚数を管理する必要がある
かんばんがある限り、在庫はゼロになりません。
また、生産を打ち切った部品のかんばんは早急に破棄する必要があります。
生産量の増減に応じて、適切なかんばん枚数にしておかないと、ムダな在庫が増えたり、欠品が生じたりします。
・計画の大きな変動に弱い
平準化を前提としているのは、計画の大きな変動という弱点があるためです。
ちなみに、トヨタ自動車の 1か月前内示の精度は、90%を超えます。
他の自動車メーカーの精度は、ひどい場合には50%程度のときもあると、嘆く部品メーカの方を多く知っていますが、そうなると、カンバン方式では回せません。
平準化をせずに、カンバン方式を導入すると、協力会社への負担増大になってしまいます。
カンバン方式に適した業種
カンバン方式はシンプルな方式なので、どのような業種でも適用可能です。
多品種の生産管理も上手にこなすことが出来ます。自動車関連でなくとも多くの業種で利用されています。
また、カンバン方式の導入を指導してくれるコンサルタント会社も多く存在します。ボードゲームで、カンバン方式を実践的に体験するセミナーもあります。
反対に、生産の変動が大きいとか、大ロット生産がどうしても必要であるという環境であったり、賞味期限が短い「生もの」を扱っている環境では、カンバン方式は難しいでしょう。
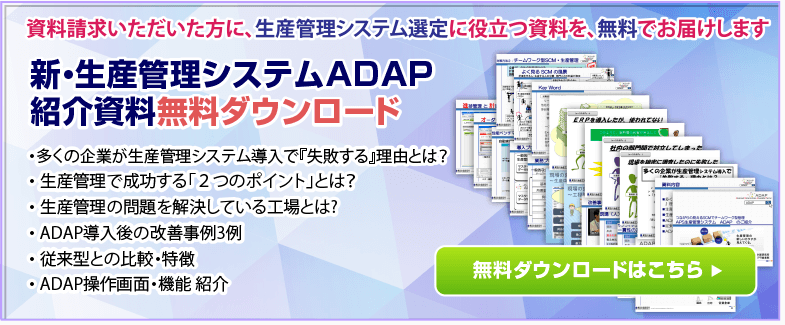
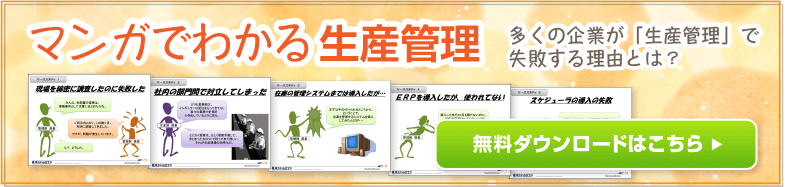
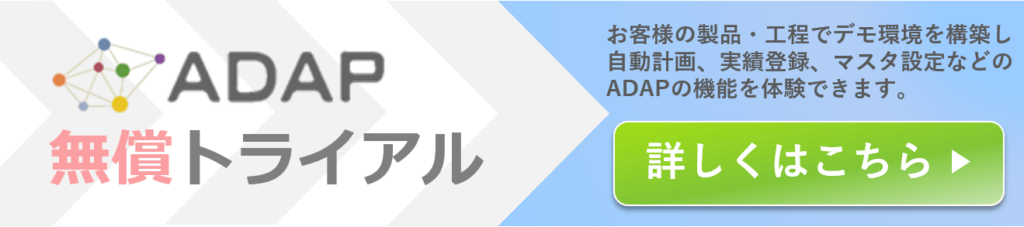