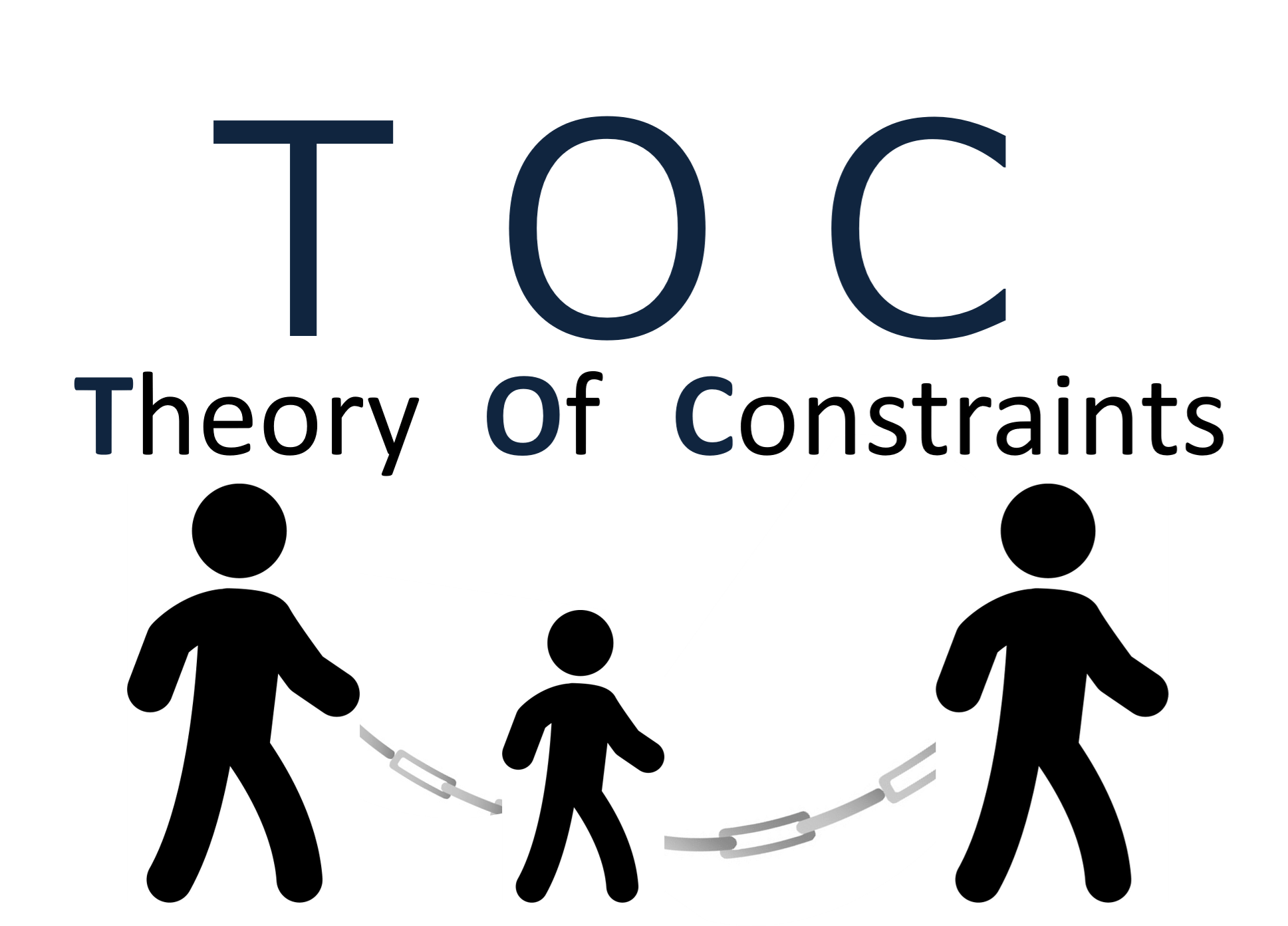
■TOC(制約理論)とは?
生産現場で「納期遅延」「過剰在庫」「リードタイムの長期化」といった課題に直面していませんか?
TOC(制約理論)は、これらの課題を根本的に解決し、生産性向上と利益最大化を実現する手法です。
TOC(Theory Of Constraints:制約理論)は、「制約(ボトルネック)を特定し、そこに合わせて全体のプロセスを最適化する」という、組織全体のパフォーマンス向上を目的とした生産管理手法です。
イスラエルの物理学者エリヤフ・ゴールドラット博士によって開発されました。
TOCを解説したビジネス小説『ザ・ゴール』は世界的なベストセラーとなり、生産管理やサプライチェーン・マネジメントに多大な影響を与えました。
■TOCが生まれた背景:MRPの課題
TOCが注目される以前は、MRP(Materials Requirements Planning:資材所要量計画)と山崩し(スケジューリング)がシステムによる生産計画手法としてメジャーでした。
MRPと山崩しの不整合を解消するために、クローズドループMRPなどの手法も提唱されていました。
MRP(資材所要量計画)
これらの手法はいずれもリードタイムが長くなり在庫が増えてしまうという課題を解決できていませんでした。
所要量計算をしなければ、どれだけ山を崩さなければいけないか分からないけれども、所要量計算したあとでは、山崩しとの不整合の発生を根本的には解消できません。
そんなジレンマに悩んでいた生産計画システムに対し、TOCは画期的な解決策を提示しました。
■TOCによる生産管理の変革:ドラム・バッファ・ロープ(DBR)とは
TOC理論は、これらのMRPの課題を解決する理論として登場しました。
ゴールドラット博士が開発した生産管理システム「OPT(Optimized Production Technology)」に、このTOC理論が組み込まれました。
また、「ザ・ゴール」という小説で理論の内容が説明されています。
その中心となるのがドラム・バッファ・ロープ(DBR)です。
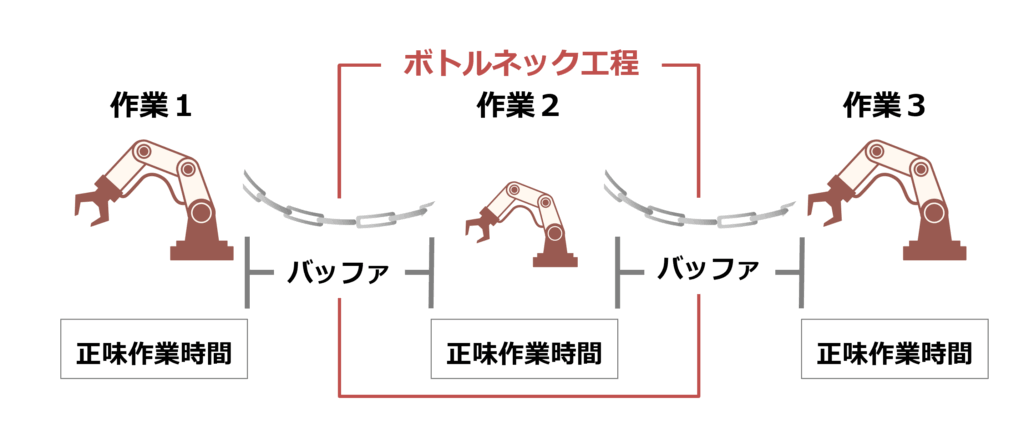
- ドラム(Drum): 生産ライン全体のペースを決める「ボトルネック工程」の生産スピード。
- バッファ(Buffer): ボトルネック工程の前後に設けられる時間的な余裕。ボトルネック工程の稼働率を下げない効果があります。
- ロープ(Rope): 全ての工程がボトルネック工程にシンクロするための制約。バッファがロープの長さを超えないように制限します。無駄な仕掛品の発生を防ぐ効果があります。
ボトルネック工程の所要時間は「正味作業時間」と置き、ボトルネック以外の工程は、その処理能力に余裕があるため、バッファ分だけずらしてネック工程に合わせてシンクロさせます。
まず、納期から後工程のリードタイム(=正味所要時間+バッファ)をマイナスして、ボトルネック工程の終了日程を決定します。
その後、ボトルネック工程の山崩しを行い、開始日程を決めます。
その他の工程はボトルネック工程とバッファだけずらしてシンクロさせます。
つまり、このDBRの考え方では、ボトルネック工程を100%活用し、他の工程をシンクロさせることで、スループット最大かつリードタイム最短・在庫最小化を目指します。
このように、TOCの根幹にあるのは、「全体最適」の考え方です。
部分的な効率化を追求するのではなく、ボトルネックを特定し、そのパフォーマンスが最大限になるように努めることで全体パフォーマンスの最大化を図ります。
ボトルネック工程以外の稼働率を高めてもスループットは向上せず、むしろ、過剰な仕掛品が発生し、コスト増や品質問題につながる可能性もあります。
TOCは、このような部分最適の罠を避け、常に全体を見据えた改善を促します。
■TOCとトヨタ生産方式の違い
TOCと並んで少ない在庫で運用できる生産方式としては、TOCの他にトヨタ生産方式のカンバン方式が有名です。
両者には共通点もありますが、アプローチに違いがあります。
TOC:制約(ボトルネック工程)のスケジューリングに合わせて全体工程をシンクロさせる。
カンバン方式:後工程引き取り方式により、全体工程をシンクロさせる。
カンバン方式とは メリット・デメリット
どちらの理論もスループットを最大化したうえで、リードタイムと在庫を最小化するための生産方式です。結果、ROA(Return On Asset:総資産利益率)が最大化されます。
■APSへの発展とTOC
TOC(制約理論)は、多くの研究者・実務家に強烈な刺激を与え、更なる改良の試みがなされました。その中の一つに、APS(Advanced Planning & Scheduling :先進的な生産計画とスケジューリング)と呼ばれるものが登場しました。
APSでは、ボトルネック工程を自動的に特定したり、プロダクトミックスによってボトルネックが変動する場合にも対応できるように改良が加えられています。
リードタイムの短縮、仕掛在庫の削減に大きな効果があり、短納期対応を可能にし、ROA(総資産利益率)を高める生産管理を実現します。
APSとは 生産管理に適用するメリット
弊社の生産管理システムADAPも、APSの考え方を組み込んだシステムの1つです。
全体最適となるような適切な計画を立てるとともに、状況の変化に応じた機敏な計画変更(イベント・ドリブン)に対応できる、システムです。
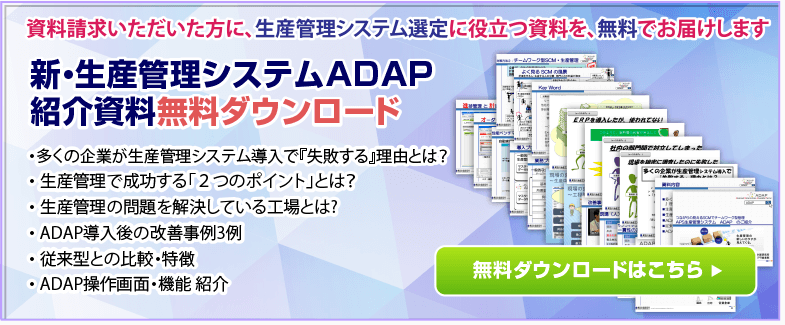
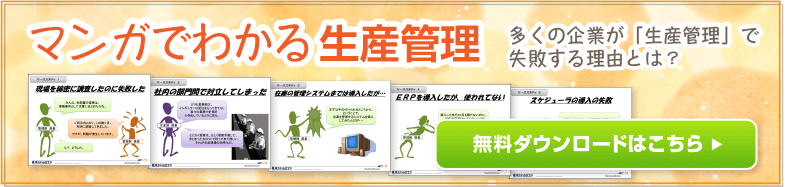
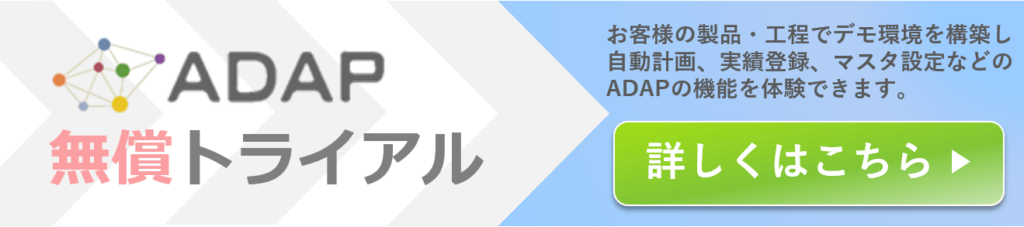